The process of sintering metallic powders
After the molding of the pieces, the key production process begins: sintering.
This process transforms the compacted powder, the “green part,” into a dense solid.
In our case, this process takes place inside an 18-meter automated belt furnace with 4.0 technology (precision control, remote monitoring, remote programming, these are just some of the capabilities and functions of the new plant installed in January 2022).
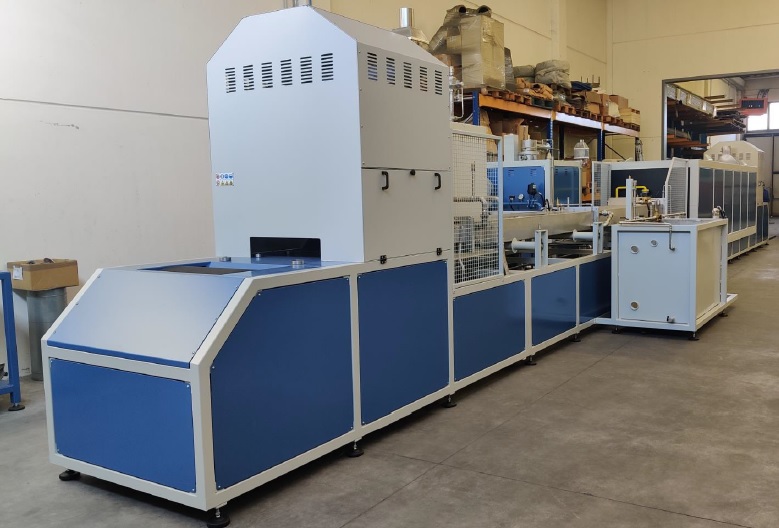
The belt furnace consists of two main sections, the heating zone and the cooling channels.
The protective atmosphere in which the parts are “immersed” during all phases of heating and cooling is crucial for the correct sintering process.
This protective atmosphere is created through an endogas atmosphere generator, which mixes air and methane in well-defined proportions.
The control system for the ratio of air to methane that creates the endogas atmosphere is essential for maintaining stable and controlled sintering.
Furthermore, the distribution system of the protective atmosphere inside the sintering furnace allows for a uniform distribution of the protective gas over the pieces.
The stages of the sintering process
Inside the heating zone, there are 6 independent sub-chambers that bring the parts up to temperature.
After an initial delubrication phase, during which the lubricants used during molding are removed, there is the actual sintering phase, during which the pieces undergo a physical-chemical transformation.
Once the transformation is complete, the parts are transferred to the cooling channels where they are brought back down to room temperature.
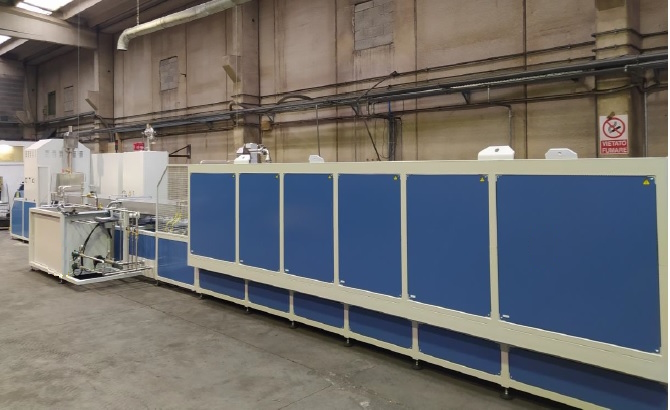
During this process, the metallic particles are heated until they reach the sintering temperature, which is usually between 1100°C and 1250°C for ferrous-based powders.
At these temperatures, the metallic particles undergo a physical and chemical transformation that leads to the formation of a compact metallic matrix.
This matrix has a porous structure characterized by a series of channels and cavities, which give sintered components excellent lubrication capabilities, particularly in the case of self-lubricating bronze or iron bushings, promoting the formation of a continuous lubricating film.
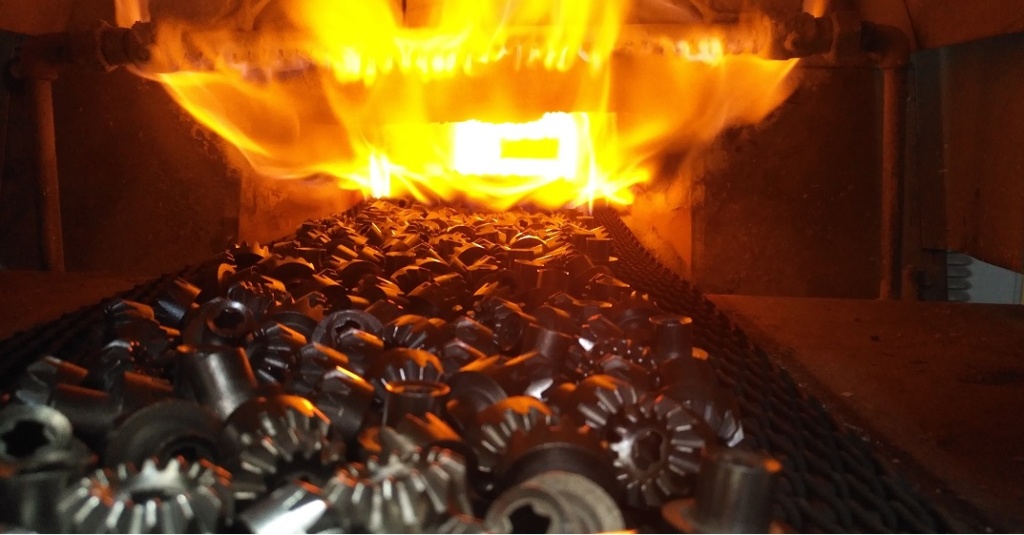
Once the thermal cycle is complete, the parts are, if necessary, ready for shipping.
This process produces materials with high mechanical properties, such as tensile, flexural, and torsional strength, high hardness, and good corrosion resistance. These properties make these materials ideal for a wide range of applications, including components for weapons manufacturing, metalworking tools, aerospace and defense components, and many others.
Gallery
Click here to see some of the components we produce.